PCI Pharma Services: Your Partner To Meet Growing Demand for Prefilled Syringes
The Growth of Sterile Injectables
The COVID-19 pandemic not only has had an exponential impact on the growth of the vaccine market, it has fast-tracked the healthcare industry’s growing acceptance of patient self-injection, enabling patients to continue treatment outside of hospital settings and within outpatient and home environments. The belief is that it will increase patient compliance as patients will not have to visit a clinic or doctor’s office for their treatment. The fast-paced development of feature-rich sterile injectable devices, which extend safer and more convenient self-injections for patients, is driving the expectant 11.95% compound annual growth rate (CAGR) through to 2030 of the global pre-filled syringe market, which was valued at $18.43 billion in 2021 (1).
Aseptic Filling of Ready-to-Use (RTU) Containers
Administered parenterally to patients, products such as vaccines and other biologics require specific and unique production processes to optimize both particulate and bioburden control while ensuring uncompromised sterility throughout the manufacturing process to maximize patient safety. This has led to the development of aseptic processing and containment methods to better protect drug products from contamination for both clinical and commercial-scale sterile injectable products.
As a result, the industry is looking for advanced ways of improving efficiency, reducing cost, and increasing sterility assurance, thus leading to robotic processing gaining huge popularity for the primary filling of ready-to-use (RTU) containers such as vials, syringes, and cartridges. Advances in filling technologies, combined with increased development of parenteral drugs and the benefits of patient-centric delivery devices to patients, healthcare professionals, and drug manufacturers, compared to traditional vial and syringe drug-delivery options, are driving significant growth of new and advanced device formats across the pharmaceutical industry, particularly the use of pre-filled syringe (PFS) technologies.
Drivers of Pre-filled Syringe Growth
Several factors are driving growth in pre-filled syringes as outlined below.
1. Market growth for biologics and biosimilars
Biologic drug products, including vaccines, are rapidly replacing traditional solid oral dose treatment options based on their increased efficiency, efficacy, as well as patient safety with reduced side effects. The biologics market is growing at a CAGR of 9.22% per year through 2027 (2). Likewise, some of the most prescribed biologic products, have recently, or will shortly, lose exclusivity in the market, leading to the appearance of lower-cost biosimilars, further boosting market growth.
2. Growth of chronic diseases
The majority of drugs delivered by pre-filled syringe are used for chronic diseases such as diabetes, rheumatoid arthritis, and multiple sclerosis. According to the International Diabetes Federation report, the number of people aged between 20 and 79 globally living with diabetes was estimated at 537 million in 2021 and is expected to increase by 46% to nearly 784 million by 2045 (3). A large patient base, a growing prevalence of diabetes, and the need for effective and safer insulin-delivery devices are some of the factors contributing to the diabetes segment dominating the scope of pre-filled syringe use, with around 53.75% of the revenue share (4).
3. Ease of use
One of the biggest drivers in the movement to pre-filled syringe technology is the desire to make products easier to use. Whether in emergency medicine in a hospital setting or at home by patients, there is an increasing desire for efficiency and ease in delivery of parenteral medicines.
- Patient benefits
Patient convenience is dramatically improved when drugs can be safely administered at home, eliminating travel time and doctor/hospital visits. Not only does self-administration eliminate the cost of injection in a clinical setting, but pre-filled syringe technology makes self-injection easier. In addition, specific unit-dosing provides enhanced accuracy compared to the traditional vial and syringe format, thereby improving patient compliance and outcomes. This is particularly important for our growing aging population who may have reduced dexterity and failing eyesight.
- Healthcare provider benefits
Healthcare providers benefit from the ease and speed of administration, which can be lifesaving in emergency situations. Advances in needle-safety devices such as needle guarding caps and retractable needle systems aid in reducing stick injuries to those administering vaccines and other injectable treatments and also the disposal of spent needles.
4. Reduced drug-product waste
Utilizing a pre-filled syringe dosage form eliminates the waste caused by overfilling vials, which can be as high as 15 to 25%. This is not the case with a pre-filled syringe format as the design, components (including stoppers), and functionality improve dosing control, thereby significantly reducing drug-product waste. Combined with advanced robotic aseptic pre-filled syringe filling technologies, which deliver minimal line losses as low as 50 mL, these technologies provide a significant increase in available drug product for the patient population. As a result, pre-filled syringe formats are associated with lower manufacturing costs despite the initial higher cost of goods versus vials.
Eliminating or reducing drug product waste is a particularly important consideration for high-value drugs such as biologics, life-changing orphan drugs, and for vaccines in critically short supply.
Meeting the Demand for Scalable Sterile Injectable Services
As more drug products move from vials to syringe dosage forms, the need for syringe-filling capacity is growing steadily. In response to the evolving biologics industry landscape and as part of PCI Pharma Services’ global strategy to increase our sterile fill–finish capabilities and alleviate the global capacity shortage for sterile drug manufacturing and innovative injectable packaging, we continue to invest and grow our service offerings through acquisition, investment in state-of-the-art technology, and our people.
In December 2021, PCI Pharma Services acquired Lyophilization Services of New England (LSNE), a premier Contract Development and Manufacturing Organization (CDMO) headquartered in Bedford, New Hampshire. The acquisition was a key step for PCI as LSNE expanded the breadth of our services as a global, integrated CDMO, building on our expertise in specialty manufacturing, clinical trial supply, and commercial pharmaceutical packaging. PCI now offers integrated large- and small-molecule solutions for clinical and commercial clients, including global manufacturing capabilities in complex formulations, high-potency compounds, sterile fill–finish, and lyophilization.
Increased Emphasis on Closed Sterile Robotic Processing
Gloveless, closed systems with robotic handling, filling, and closure processes that provide a high level of sterility and fill accuracy are emerging as key, and PCI Pharma Services is leading the way by investing in these technologies to further enhance our global sterile fill–finish operations to support our clients.
Robotic Aseptic Platforms at PCI Pharma Services
Complementing our global sterile fill–finish and lyophilization manufacturing capabilities across North America and Europe, PCI has invested significantly in these state-of-the-art robotic technology platforms at both our San Diego, California, US and Melbourne, Australia facilities. These technologies are positioned at locations where a high volume of early-phase clinical trials take place and also allow our clients to benefit from the 43% tax rebate incentive for clinical trials conducted in Australia.
Utilizing the latest advancements of the Cytiva Microcell and SA25 technologies, we deliver flexible aseptic fill–finish solutions for both small and larger-scale production runs across a variety of dosage forms, including vials, pre-filled syringes, and cartridges for use in auto-injectors, helping to meet our clients’ needs by delivering products to patients safely and efficiently. Our investment in multiple robotic technologies provides a scalable solution for our clients, meeting clinical trial drug-product requirements from early Phase I trials and beyond. These systems are also helpful in minimizing product loss during filling by utilizing minimal hold-up volumes and reducing overall manufacturing costs, particularly critical when processing high-value biologic therapies.
The Microcell platforms in San Diego and Australia offer fully automated, gloveless filling, performed through closed robotic isolator technology that provides both small batch flexibility and standardized manufacturing. The fast changeover and agility of the technologies make it suitable for the production of both personalized medicine batches and clinical trial supplies, delivering true speed to patients. Superior drug-product quality is assured through advanced automation, removing the need for operator intervention during the filling process and limiting product contact. Importantly, the Microcell technology can fill up to 1,200 units per batch with fill volumes ranging from 1.0–50 mL.
Providing a scalable aseptic solution in support of clients progressing through the clinical lifecycle toward commercialization, the SA25 Aseptic Filling Workstation is a larger-scale, gloveless, isolator-based filling technology offering small- and large-scale batch production of up to 20,000 units, supporting fill volumes from 0.2–50 mL. It provides flexible manufacturing solutions with the ability to fill multiple delivery device formats, including vials, syringes, and cartridges through an aseptic process.
For both the Microcell and SA25 technologies, precise, programmable robotic functions cover all aspects of the fill process, including isolator leakage tests, VHP sterilization of the container closures, filling into the container-closure system (CCS) of choice, capping, and batch delivery. They are also compatible with ready-to-use (RTU) containers and closures, removing the container and closure preparation stage, aiding speed of delivery of a quality and sterility-assured drug product.
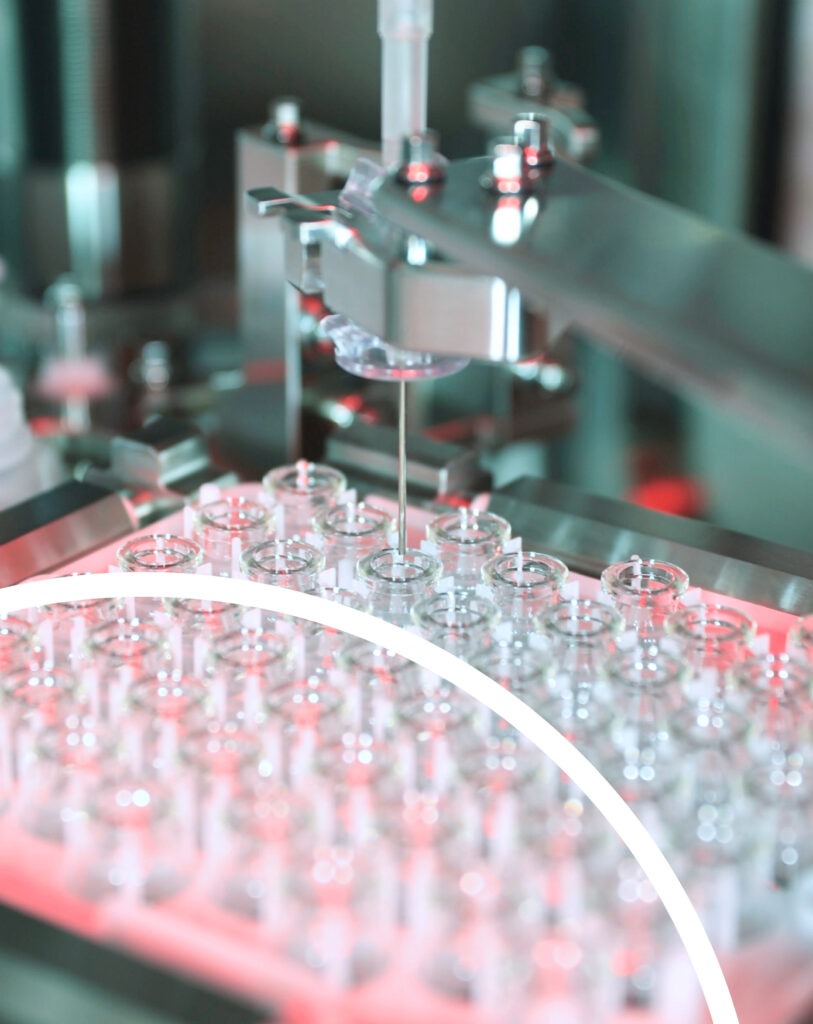
Robotic Advantages for Our Clients
The robotic processes provide several key advantages as outline below.
Speed and accuracy
Expediting the filling process with automation while also increasing accuracy, the robotic platforms with high-precision Dynamic Peristaltic Pumps ensure accurate fill volumes with minimal product losses. These pumps are also a gentler method of filling, creating less sheer on biologic products than positive displacement pumps. This is a significant benefit to our clients, who are often developing life-changing, high-value drug products with the need of progressing through the clinical pipeline with efficiency and speed. Minimizing product losses not only conserves valuable drug product and therefore reduces costs, but also ensures our clients’ clinical supply needs are met and key milestones are achieved as the product progresses toward commercialization.
Quality and sterility assurance
Isolators represent the superior choice in terms of sterility and elimination of risks. With a robot performing the processes in a recipe-driven, validated system and utilizing single-use parts, pre-sterilized flow paths and RTU containers, multiple sources of risk are eliminated, including: potential cross-contamination, human error, electro-mechanical filling and closure activity failures, environmental control failures, cleaning and set-up errors,and product loss.
Using press-fit vial closures with integrated rubber stoppers not only reduces the risk of particle contamination but also simplifies the manufacturing process with the press-fit closures being a one-step application that presses closures on top of the vials, versus the traditional two-step process of stoppering and aluminium crimp capping. All this combined means our clients are able to move more rapidly through the clinical stages and provide safe, life-changing therapies to patients.
Flexibility
Robotic technologies are designed for maximum flexibility while maintaining high aseptic processing rates. Meeting the needs to fill many different products and process multiple projects with minimal changeover time between batches provides the ultimate savings in time, allowing us to better support clients who have urgent drug-product supply needs.
Seamless Sterile Solutions
Our clients have the aim of accelerating their sterile drug-development lifecycle and seek readily available capacity to reduce time to clinic and ultimately commercial launch. They seek experienced partners able to meet their fill demands with state-of-the-art technology to minimize the risk of failure, particularly in the early-stage development of complex, high-value products that by their nature can be difficult to handle. Any failure during the aseptic fill-finish process can lead to product degradation affecting a drug’s efficacy and patient safety. The importance of mitigating risks cannot be overstated: failure in a batch can mean significant time to replace it at substantial cost, and may put the entire timeline in jeopardy, delaying clinical trials, launch plans, commercialization and ultimately impacting patient lives.
Providing integrated end-to-end solutions and helping to reduce supply-chain complexity and risk, our clients can also access our expert secondary packaging, labelling, and distribution solutions available across our extensive global network, leveraging the benefits of with working with a single supplier. Combining our expertise in sterile fill–finish manufacturing with specialist biologic packaging, labelling, and cold-chain distribution provides a valuable end-to-end solution, simplifying the supply chain while delivering time and cost efficiencies.
Planning for the Future
As more new biologically derived therapies such as antibody, mRNA and sRNA treatments are discovered, the need for specialized sterile fill–finish manufacturing and innovative packaging capabilities and capacities will continue to increase.
Meeting these growing capacity needs of the industry, PCI is continuing to invest and provide strategic manufacturing and packaging solutions for our client partners. With a $100-million investment, we will have enhanced our integrated development to commercialization sterile fill–finish offering with a new commercial-scale facility at our Bedford, New Hampshire, campus, providing increased capacity using state-of-the-art isolator technology, including high-speed, large-volume sterile fill–finish and lyophilization lines with multiple 400-ft2 freeze dryers.
Supporting the downstream supply chain and the growing biologic market’s need for specialized packaging for injectable drug delivery device combination products, we are also investing $50 million in a new 200,000-ft2 facility at our Rockford, Illinois, site. This new facility will support the assembly and packaging of vials, pre-filled syringes, auto-injectors, and pen-cartridges such as those for glucagon-like peptide 1 agonists (GLP-1) for the treatment of diabetes and obesity.
With both manufacturing and packaging facilities to be operational by Q3 2024, capacity reservation is available immediately to our clients, helping them strategically plan their product outsourcing with a single integrated CDMO. As a leading global CDMO through innovative integrated solutions, we aim to reduce time to market and de-risk our clients supply chain, delivering true flexibility and excellence in all that we do to accelerate the development and commercialization of life-changing therapies.
References